The uses and limitations of oil containment booms
- Oil containment booms provide good buoyancy, sealed in PVC and light weight
- However, they do not absorb oil
- Some alternatives can be sorbent booms, debris booms
A foam filled containment boom is a boom designed to contain oil spills where the foam provides the buoyancy for the boom to float on the water. Oil is cleaned up by skimmers or vacuum systems. Pros and cons of foam filled containment booms are summarised as follows:
Pros | Cons |
---|---|
Good buoyancy |
Must be used along with skimmers or absorption pads |
Foam is sealed in PVC to avoid leaks |
|
Lightweight |
Foam filled containment booms are primarily used as a first response to contain the oil spill in a cordoned off area, after which clean up operations can be executed. Containing the oil in a small area concentrates the slick into a thicker layer and makes the removal process easier.
Foam filled containment booms have great buoyancy
The critical performance characteristic of containment booms is their ability to float on the surface of a body of water, thus preventing oil from spreading beyond the boom. Different designs can be used depending on whether the water is flowing, the boom is being towed, or the boom is deployed in standing water:
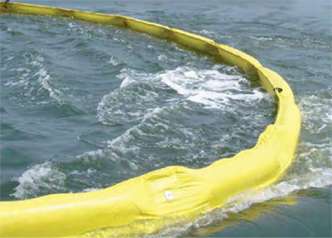
SuperMax boom
- OptiMax booms are used in fast moving water and near shore conditions. The extra buoyancy of these booms ensures effectiveness even when the water is fast moving.
- SuperSwamp booms are used in streams, canals and roadside ditches.
- Simplex booms are an industry standard for use in shoreline and protected waters.
- SuperMax booms are designed for use in harbours and open waters.Foam filled booms are sealed in PVC to prevent foam leakage
Oil spill control and clean up operations happen in robust environments that can cause damage to equipment. Foam filled containment booms are sealed in PVC sleeves in order to prevent or limit this damage. PVC is a hardy fabric, resistant to sun damage and tearing.
Additional components are added to booms to protect them from damage. Tension wires and chains absorb the pressure of fast flowing water so that the PVC does not stretch to the point of breaking. Handles enable contractors to move the booms easily. Anchor points are provided to secure the booms to the ground and thus keep them in position.
Foam filled booms are lightweight
As a first response oil spill equipment, it is important that foam filled containment booms are light and easy to deploy. SuperSwamp booms are the lightest of the available options with a weight of 1.1 kg per meter, while the standard Simplex booms are about 2.5 kg per meter. The weight of SuperMax and OptiMax booms vary depending on the height from 1.8 kg per meter to over 6 kg per meter.
Foam filled booms do not absorb oil
The most significant disadvantage of foam filled containment booms is that they do not absorb oil, they only contain it while it is being removed.
Typically, oil skimmers will be used with foam filled containment booms to perform the clean up operation. Oil is skimmed from the surface of the water inside the contained area. Once all the oil is removed, the foam filled booms are removed from the area.
What alternatives are there when foam filled booms cannot be used?
Foam filled booms are not suitable when containment and absorption are required.
Sorbent booms are made of a material that absorbs oil, while repelling water.These booms remain afloat even when fully laden with oil. Sorbent booms are costlier than foam filled containment booms because of the special absorbent material used.
Fire booms are used to contain oil, which is then burnt off the water rather than removed through skimmers. Fire booms are not used often and only in circumstances where the spill is large and conditions require burning to minimise other negative environmental consequences. Fire booms can sustain the high temperatures of hydrocarbon fires without being damaged.
Debris booms are semi-permanent installations that prevent debris from entering a sensitive water environment. These booms are used to protect Sydney’s water from floating debris.
Foam filled containment booms success story
In April 2017, a rupture in an undersea pipe caused an oil spill in Port Moresby harbour. The South Pacific Emergency Response Centre deployed foam filled containment booms to great effect in order to restrict the spill are until clean up operations were complete.
Contact SpillPro for more information about foam filled containment booms.
SpillPro has extensive experience in oil spill containment. We have a variety of foam filled and other containment booms for any application. Our technical experts and proven solutions can help your business overcome the challenges of managing spills.
Call our expert team on 1800 368 450 today to discuss the best containment boom solution for your business.
Must Read
SpillPro on 24 February 2025
Why Spill Readiness Matters
A spill isn't just an inconvenience. If not handled properly, it can lead to safety hazards, environmental damage, and compliance issues. By equipping your site with the right spill response solutions ...
Read moreSpillPro on 30 October 2024
Choosing the Right Containment Boom
Containment booms are the first line of defence in any spill response plan. When a spill occurs, swift and effective containment is crucial to minimise environmental impact and financial loss. Selecti ...
Read more